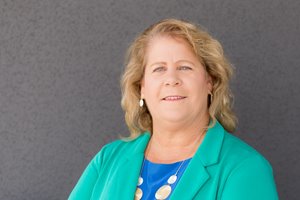
Angie Simon, SMACNA President
The economic recovery continues as we manage the new jobsite reality of additional processes and procedures to help combat the transmission of SARS-CoV-2. My virtual and now in-person visits with members have revealed that there is more focus on the jobsite, especially through two lenses: what keeps our people safe and what can help keep projects on time and on budget.
We are not the only ones focused on these goals.
The construction jobsite is gaining more attention than ever from manufacturers, suppliers and technology companies looking to provide solutions to our challenges. This focus on jobsite safety is generating solutions that make work safer, more efficient and more cost effective.
With the onset of COVID-19, contact tracing on jobsites has become a necessity that many have turned to technology to address. Whether it’s an app on a phone or a mobile device attached to clothing, tracking movements within the jobsite is now more commonplace. Some technology companies are taking it a step further, studying efficient movement and organization on jobsites to help contractors effectively schedule crafts persons and maximize productivity over the course of an entire construction project.
One of the devices featured in the issue measures jobsite progress. It “walks” a job site, measures changes via 3D laser imaging and reports progress to the project team, thereby eliminating the need for multiple people to walk the jobsite to verify what work has been completed and what areas are ready for the next stage — a great productivity tracking tool!
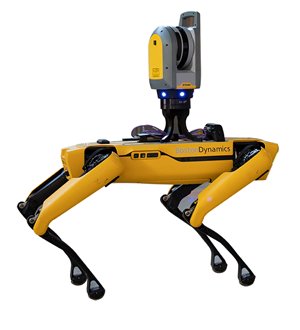
Another new technology is the robot that drills holes for our hangers. This hits what I call the sweet spot, combining improved safety with increased efficiency — a goal we contractors all like to accomplish.
Operated by a single craftsperson, this “cobot” can drill up to 700 holes per day in a ceiling slab (on a good day my field can manually drill 120 holes). That is 700 less opportunities for a person to get hurt climbing a ladder or operating a scissor lift. It also removes the possibility of repetitive motion shoulder or back injuries. The ability to drill 700 holes in a day is also a productivity eye-opener. Getting the job done quicker and safer is something our industry should always try to achieve.
The last technology we cover in this issue makes me think of a car assembly line. It’s a new coil line that takes rolled sheet metal, cuts it, creases it, folds it and applies insulation. The laser cutter is now part of the coil line and makes all cutouts necessary to speed prefabrication and assembly. Very efficient and a great time saver — as we all strive to become more productive in our shops.
SMACNA remains committed to educating members on technology impacting our industry. Bottom line: Thoughtful technology adaptation helps keep us competitive as well as safer as an industry, while expanding our capacity to better serve our customers.
Sincerely,
Angie Simon, SMACNA President